Development Story
Automotive Transmission Belts
The Story behind the Development of the "Low Friction Loss Belt"
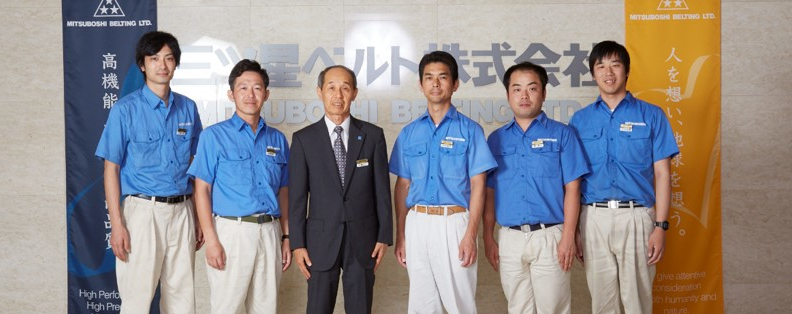
The "Low Friction Loss Belt," the World's First Accessory Belt to Achieve Low Fuel Consumption and Noise Generation Resistance
In the Japanese automotive industry, competition to reduce fuel consumption is becoming increasingly fierce. To meet these demands, Mitsuboshi Belting has taken the global lead by succeeding in the development of a Low Friction Loss Belt for accessory systems. By reducing the amount of heat generated in the belt rib section, we have succeeded in stemming the loss of flexure due to twisting and deformation. By reducing the fuel consumption associated with accessory belts, which are one of the some 30,0000 parts that make up an automobile, this breakthrough product also helps lower noise generation and friction resistance, leading to its uptake by a growing number of automakers.
But can a simple accessory belt actually contribute to reduced fuel consumption? How did we succeed in developing a Low Friction Loss Belt-something that both our customers in the automobile industry and our own engineers thought to be impossible? Mitsuboshi Belting's development team-a group of specialists from our materials development, design, assessment and sales technology departments-tells the story of this development over the course of approximately three years.
Chapter 1
The Start: An Accidental Success That Got the Engineers Thinking
A result no one had expected led us to think we might have the potential for creating a world-first product.
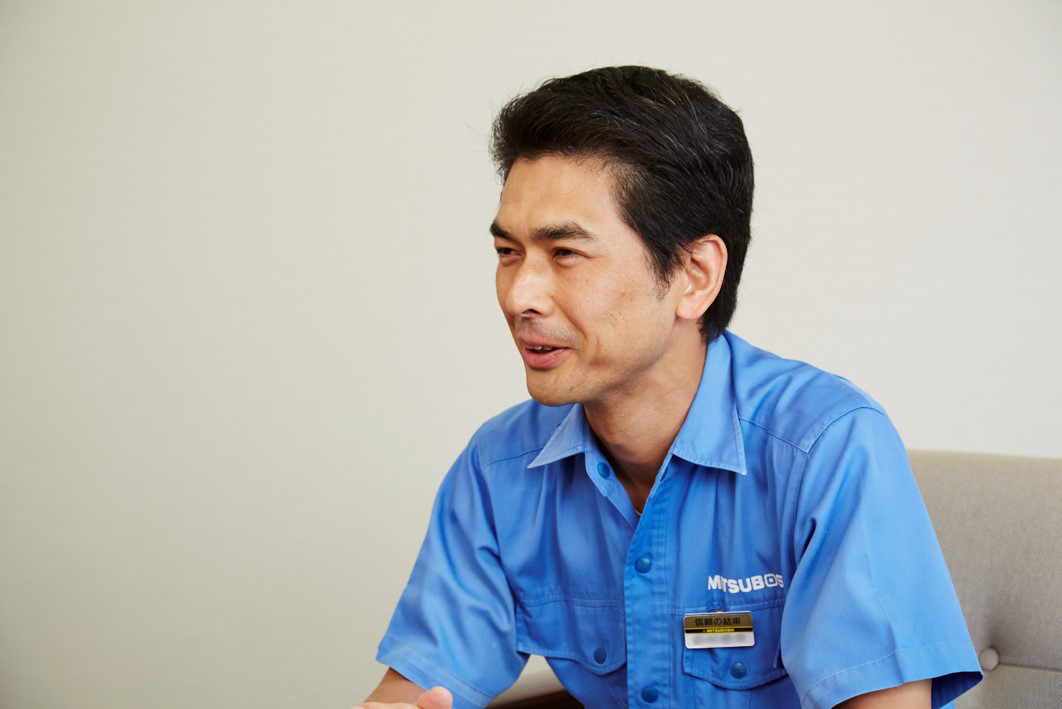
Development began when a business partner asked Masashi Tamura, the sales technology contact person for automakers "Don't you have an accessory belt that can somehow help lower fuel consumption?" He proposed using one of Mitsuboshi Belting's standard-specification products, a ribbed belt with a rubberized back. Although it was common for Japanese manufacturers to use accessory belts with cloth backs, before joining the Sales Technology Department, for many years Mr. Tamura had been working as an engineer in belt design, and he believed that rubber would provide good flexibility, and that flexure would help reduce energy loss. However, he notes that "Truthfully, my expectations were not high." Although a focus for parts on the engine itself, considering fuel efficiency improvements involving belts for generators, air conditioners and other peripheral equipment was just something not normally considered at that time. But testing produced unexpected results. The belt succeeded in reducing fuel consumption by around 0.2%. The person in charge of design at the manufacturer was also surprised that a belt could have such an effect on lowering fuel consumption. The savings was less than 1%, but for the automotive industry, focused as it was on technologies for lowering fuel consumption, even such a small savings was meaningful. Unfortunately, the proposed belt was rejected as being too noisy, but this was now a different problem. If we were only able to eliminate the noise issue, we could provide a groundbreaking product that was technically superior to that offered by our competitors. Mr. Tamura was suddenly convinced that this development was worth a try.
Embodying the corporate culture of "just give it a go," we put together a development team of members from various departments and set out to create a world-first product.
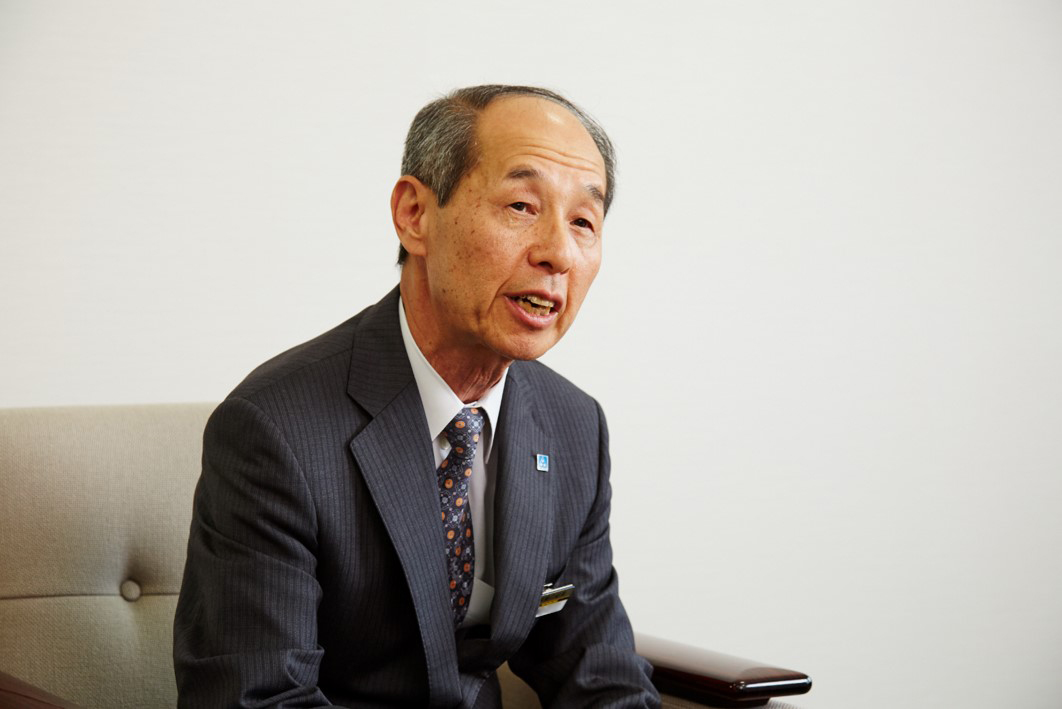
The team went right to work sounding out various technology departments about rubber compounding, belt design, analysis and other topics and asking them to contribute members to the development team. Looking back, upon hearing Mr. Tamura's thoughts, materials technology veteran Yorifumi Hineno recalls thinking "This is certainly an idea we haven't considered before, but surely it will be difficult to create a compound rubber that achieves both low fuel consumption and noise generation resistance. Typically, these are incompatible goals." Mr. Hineno was not alone. Masayoshi Nakajima, the managing director who
headed the Technology Department, and many others thought this was a wild goose chase. Still, they kept faith with Mitsuboshi Belting's forward-looking manufacturing traditions of "just give it a go." Nobody opposed giving the idea a try.A development team was formed. Hisato Ishiguro, Mr. Hineno's subordinate in the functional development department, was in charge of rubber compounding. Hiroki Imai, from the product technology department, was to handle the production of belts for evaluation and conducting physical property evaluations. Takayuki Shige from the testing department was selected to evaluate friction loss measurements, and Masashi Tamura was assigned to provide overall development direction. Hisato Ishiguro and Hiroki Imai had only recently joined the Company, and Mr. Shige had just been relocated to another department, but they were also called upon to take part in this challenge to develop a world-first product.
Chapter 2
Bringing All Our Technologies and Knowledge as a Belt Maker to Bear in Solving the Puzzle
What about a belt might be effective at reducing fuel consumption? The first step in development was to answer this question.
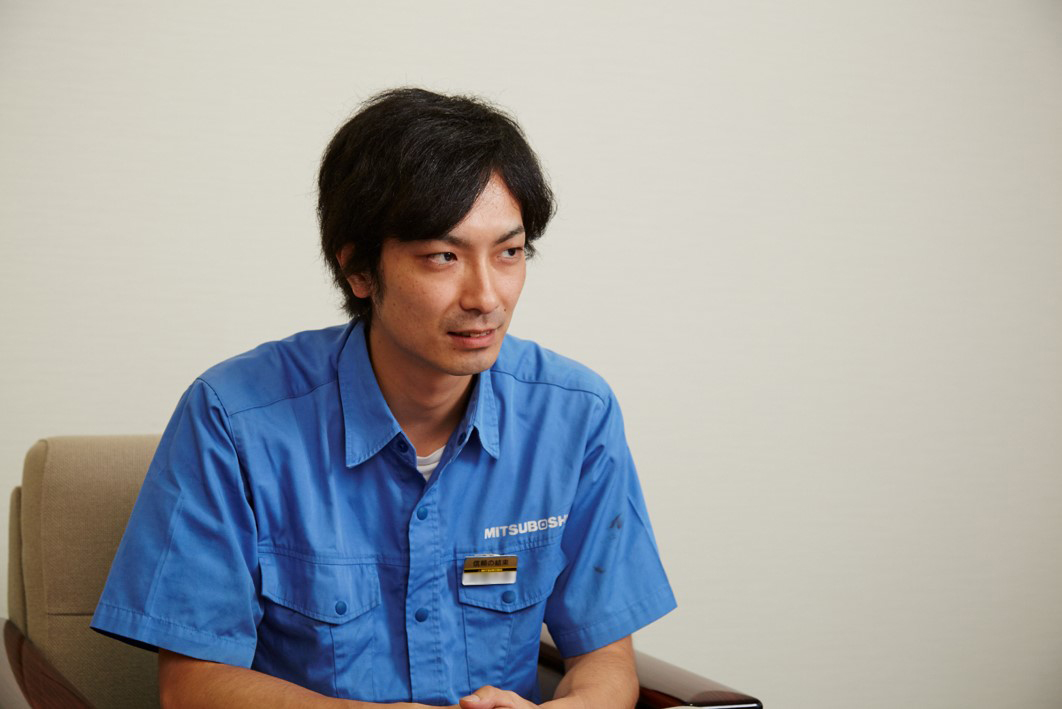
The first step was to determine which of a belt's three constituents-backing, ribs and core wire-prompted a loss of flexure and theorize why this might be. The person assigned to verify theoretical concepts regarding this reduction was Hisato Ishiguro, who had joined the Company two years earlier. Mr. Hineno chose him on the precept that "People who have long experience in designing rubber compounds are likely to have fixed ideas. To come up with altogether new technologies, we need somebody without any preconceived notions." Never having expected to be involved in new product development so early on, Mr. Ishiguro was both excited at the opportunity and apprehensive about the prospect. Encouraged by the words "It's all right to make mistakes. Just give it your best shot," he proceeded according to his own reasoning and went to work analyzing rubber materials and belt data.
Another urgent issue was to establish a method for measuring friction loss. Takayuki Shige of the testing department was able to come up with a measurement method by using testing equipment designed for another purpose by the head of the technology department, which handled the development and manufacture of testing and manufacturing equipment. His first time using this equipment, he spent each day looking at the testing device's torque meter and a month trying to resolve the issue of variations in the measured results. It became possible to measure friction losses down to a precision of 0.1Nm. From there, he moved on to measure losses for each of the constituent parts of the belt. Ultimately, the team discovered that the compounding of the rib rubber had the greatest impact on reducing loss. This result came around six months after the start of development.
How could we achieve the conflicting aims of improving fuel efficiency and lowering noise generation resistance? After days of searching for an optimal rubber compound, the answer became clear.
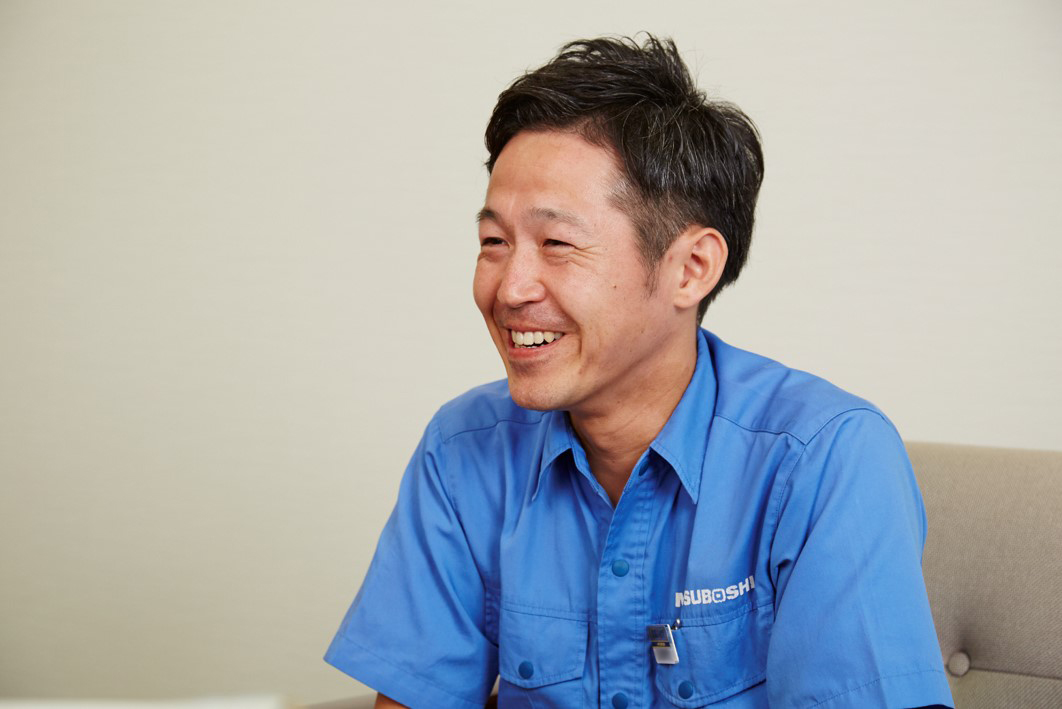
At the start of development, many of the members thought the limiting factor was not the rubber compound but rather the shape. However, once the team had narrowed down the problem to the rib rubber compound, the development vector of resolving noise generation was decided. However, eradicating that noise proved to be a thorny issue. For many years, development had concentrated on reducing internal heat buildup in the belt, but in addition to noise generation resistance these methods also caused friction resistance and productivity to worsen.
How was the team to ensure friction resistance and productivity, while at the same time achieving the noise generation resistance the customer was calling for? Hisato Ishiguro took the lead in referencing the Company's massive materials database, developing compounds through a process of repeated trial and error and then on the processing front, considering blending and rolling conditions. The process repeated: Mr. Hineno determined whether the result was viable, Mr. Imai collaborated with the factory production department to manufacture the belt for testing, and Mr. Shige conducted sound tests on actual vehicles. Repetitions continued at a fast pace, with a new iteration nearly every week. Team members were busy, as they were doing this testing alongside other tasks, but when Mr. Tamura returned from reporting development progress to the customer, all the members of the technology department gathered together, younger members and veterans alike, putting their heads together to consider the next method of attack.At the start of development, many of the members thought the limiting factor was not the rubber compound but rather the shape. However, once the team had narrowed down the problem to the rib rubber compound, the development vector of resolving noise generation was decided. However, eradicating that noise proved to be a thorny issue. For many years, development had concentrated on reducing internal heat buildup in the belt, but in addition to noise generation resistance these methods also caused friction resistance and productivity to worsen. How was the team to ensure friction resistance and productivity, while at the same time achieving the noise generation resistance the customer was calling for? Hisato Ishiguro took the lead in referencing the Company's massive materials database, developing compounds through a process of repeated trial and error and then on the processing front, considering blending and rolling conditions. The process repeated: Mr. Hineno determined whether the result was viable, Mr. Imai collaborated with the factory production department to manufacture the belt for testing, and Mr. Shige conducted sound tests on actual vehicles. Repetitions continued at a fast pace, with a new iteration nearly every week. Team members were busy, as they were doing this testing alongside other tasks, but when Mr. Tamura returned from reporting development progress to the customer, all the members of the technology department gathered together, younger members and veterans alike, putting their heads together to consider the next method of attack.Recalling an everyday saying of Chairman Nishikawa that "Developing new technologies and new products is a manufacturer's duty," team leader Mr. Tamura continued to motivate the team members. "Let's give it one more try," he would say. "I am convinced that we are going to develop a world-first belt." Even so, there were times when the sound test failed to produce favorable results that the team thought they might be permanently deadlocked on this problem. Around that time, a conference of global departmental heads from throughout the Mitsuboshi Belting Group met. The team was inspired anew by the words of President Kakiuchi that "Our company values people who go out and try new things, regardless of the results."
Finally, the team developed a compound that succeeded in reducing sound. It earned Mr. Hineno's implicit endorsement as an optimal compound, and the development moved into the final stages.
Chapter 3
The Possibilities of the Newly Developed Accessory Belt
Winning out at the last minute, the sound test was judged a success.
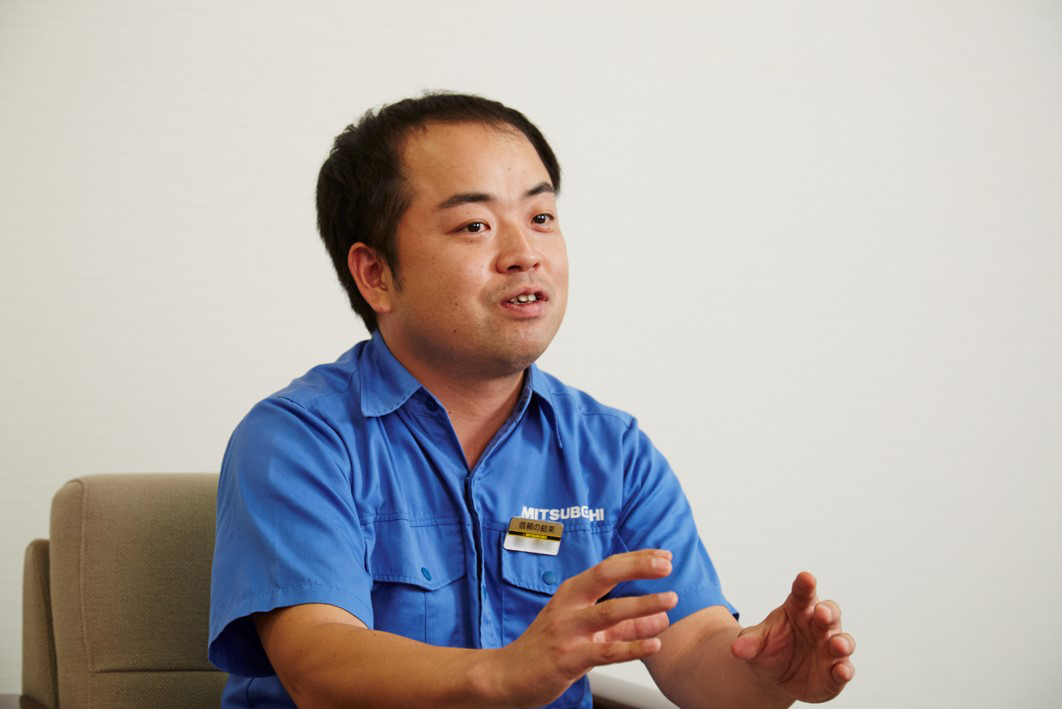
At last, a test belt produced by narrowing down rubber compounds generated positive results in in-house vehicle tests. The reduction in sound was even discernible to the ear. Although our customer had hoped to test the belt right away on a customer vehicle that was under development, they were told that the vehicle was nearing mass production, so could not be tested on that model. As proposed by Mr. Tamura and Mr. Shige, a rental car was brought in and a sound test was run together with the person at the customer end in charge of testing engine vibration and noise. The team was taking a last chance; if the belt could not clear sound tests at that stage, it would not be in time for use on the new model.
The test was run on a vehicle with a continuously variable transmission, typically a difficult proposition. During testing, the belt had been confirmed as clearing the sound levels according to conditions set by the customer, but anything was possible in a live trial. Finally the sound test evaluation results were brought to the waiting pair: "OK." They were delighted with the words of the customer representative: "That belt looks like a winner." The two team members phoned the Company to report the results to their waiting colleagues. Mr. Hineno told the team members frankly, "I am both delighted and relieved."
Finally transitioning to mass production and sales, the team moved on to the development of a next-generation Low Friction Loss Belt.
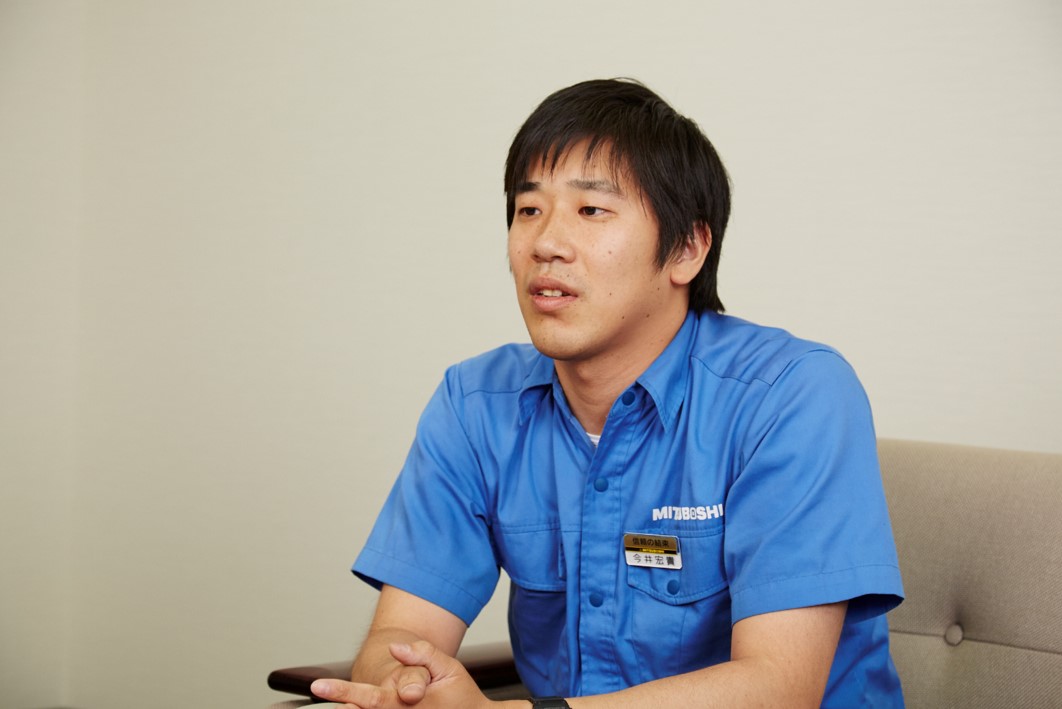
Mr. Imai, a colleague of Mr. Ishiguro, was tasked with getting the production line up and running. Looking back, he recalls "The most difficult part was summarizing the huge volume of product specifications, materials used, results, manufacturing methods and costs, taking these to an assessment meeting comprising members of manufacturing and sales, and receiving the 'go sign' on production." With the assistance of his direct supervisor and Mr. Tamura, leader of the development team, the decision was reached to begin mass production. After that point, preparations for manufacturing proceeded at a fever
pitch. Although some issues still remained to be resolved as the product went toward mass production, all the difficulty started to seem worthwhile, as new vehicle models containing the newly developed Low Friction Loss Belt began to appear on television, in magazines and on automakers' websites.Three years after the start of development, the automaker that had been pressing forward on efforts to lower fuel consumption launched its mini car. Customers gave the vehicle high marks, including for the results of fuel-efficiency calculations. During the year, the vehicle won an award for its use of fuel-efficient technologies.To date, competitors have not yet developed products equivalent to Mitsuboshi Belting's Low Friction Loss Belt, the first in the world to achieve both low fuel consumption and noise generation resistance. At the same time, Mitsuboshi Belting has continued with its successes in developing next-generation belting products that maintain noise generation resistance while contributing to even lower levels of fuel consumption. Furthermore, an increasing number of Japanese automakers are employing these products.
Thermographic Measurement of Torque Loss Conditions after the Start of Travel
This measurement shows the low amount of heat generated (little heat generated as a result of flexure) by low friction loss products.
Low Friction Loss Belt
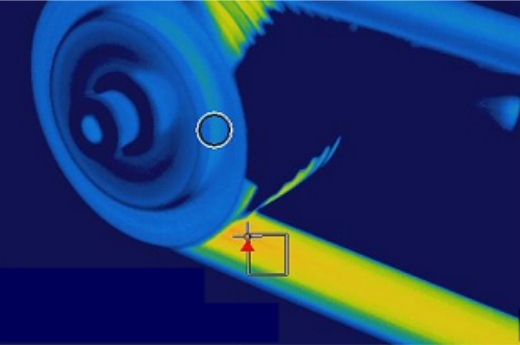
Standard Belt
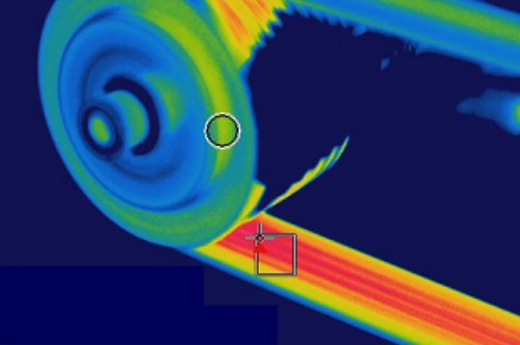
We will continue to pursue technologies in the aim of achieving even lower levels of fuel consumption.
Through their perseverance, members of the development team succeeded in uncovering new possibilities for accessory belts using technologies that nobody had considered up to that point. The successful tests did more than just boost the confidence of development team members. It also pointed toward Mitsuboshi Belting's future as a belt maker contributing to society. We believe the spirit of colleagues consistently gathering to discuss technologies is due in large part to Mitsuboshi Belting's corporate culture, which emphasizes its own new technologies. We will continue to pursue solutions to increasingly strict fuel efficiency requirements. The challenges Mitsuboshi Belting faces in expanding the use of Low Friction Loss Belts in internal combustion automobiles throughout the world is not over yet.
Team Members
If we don't tackle new developments, who will?! Maintaining Our Pride as a Belt Maker Developing World-First Belts
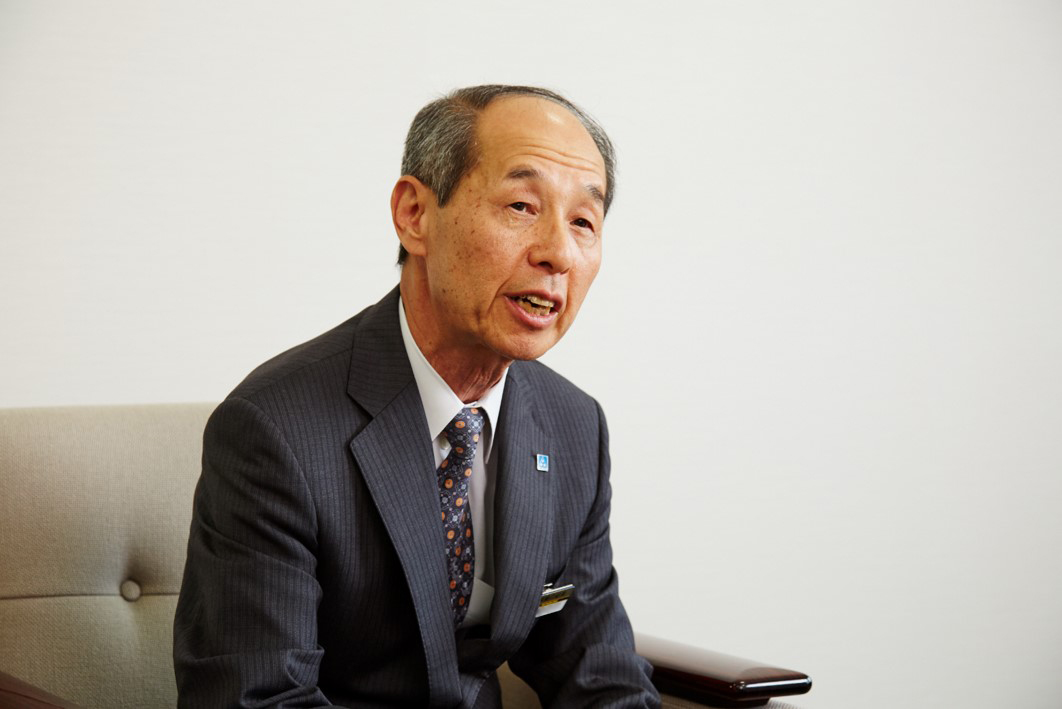
Masayoshi Nakajima
Member of the Board, Executive Officer
In charge of Technology Supervision, Industrial Materials Business Department
Our success in developing a Low Friction Loss Belt that achieved both low fuel consumption and noise generation resistance helped to boost our share of the shrinking domestic market. This development was also meaningful in the way it has helped to communicate our new technologies to the world. I always explain to our engineers that development requires work involving the head (the ability to use your head and see the big picture), heart (the tenacity to push forward) and team (the ability of all members of a team to align their efforts). I believe that these capabilities are the source of our development success and are the key to Mitsuboshi Belting's successful manufacturing efforts.
As the trend toward using smaller engines continues, the impact of belt noise is likely to increase, so better noise generation resistance is a way to add value. Having young engineers take on developmental roles early on, as we did in this project, is a way of transferring our technologies and stance on manufacturing to the next generation. I believe this approach will also lead to further technology advances in Low Friction Loss Belts.
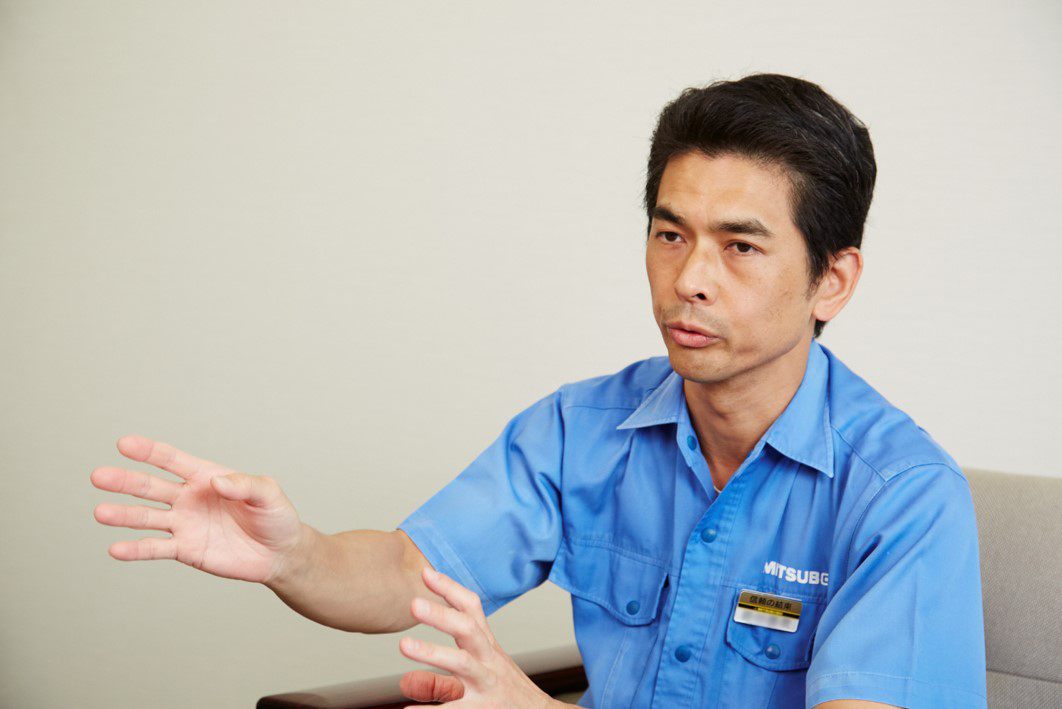
Masashi Tamura
Sales Technology Section, Product Technology Group 1,
Industrial Materials Technology Supervisory Department
I felt a real sense of achievement in our development of a world-first belt, which gave us a new foothold in the field of accessory belts. Guided by the fundamental policy of providing highly functional products offering high levels of precision and quality, we were able to quickly come up with proposals to address the problems we faced thanks to presence of experts in design, rubber compounding, test assessment, analysis and sales technology. Having these experts in place, as well as a system for developing testing and production equipment when necessary, are strengths for Mitsuboshi Belting. This project called together specialists from a variety of fields, and we were able to bring the development to a successful conclusion thanks to the cooperation and advice of many people. I started the development with information that I possessed on my own, but gained a great deal of experience and was able to grow by being involved throughout the processes of planning, development, gaining customer approval and production.
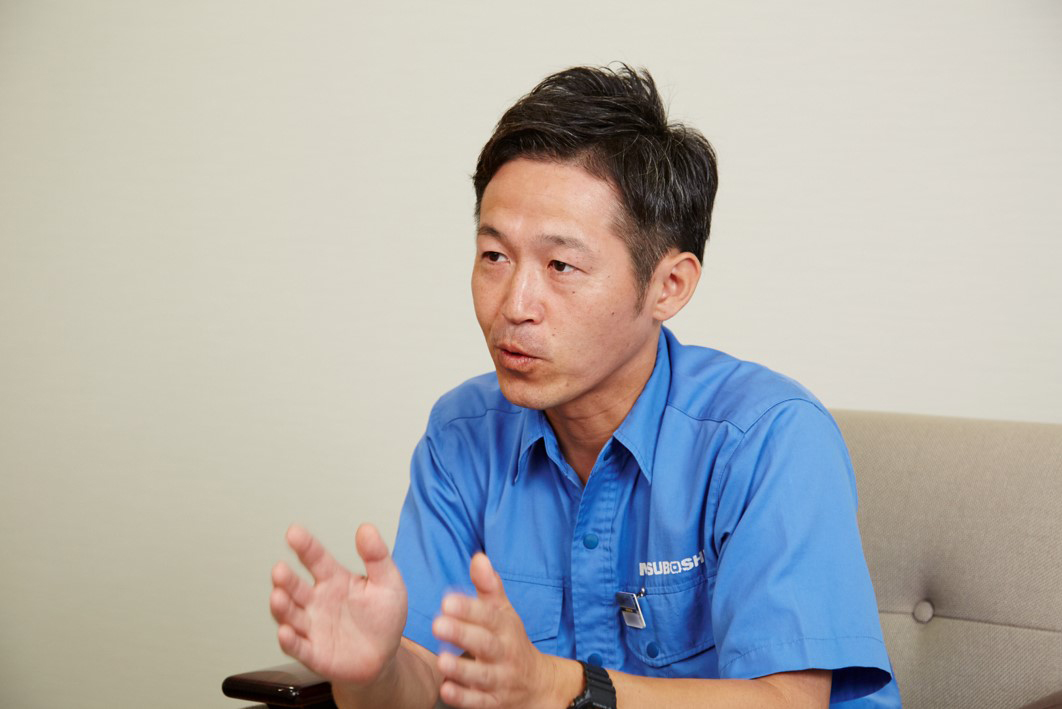
Yorifumi Hineno
Functional Development Team 2, Materials Technology Department,
Industrial Materials Technology Supervisory Department
We have a corporate culture whereby people gather to address problems, going beyond such boundaries as company background and departmental affiliation, resulting in swift execution and decision-making. I believe these characteristics are a source of strength for Mitsuboshi Belting and engender its development success. Personally, I believe it is important to remain aware of the overall development process, accurately determine turning points and prepare backup plans. Moving forward with development and receiving positive feedback from customers enhances the sense of team solidarity and allows the team to share in its sense of achievement. These are the privileges of being an engineer.
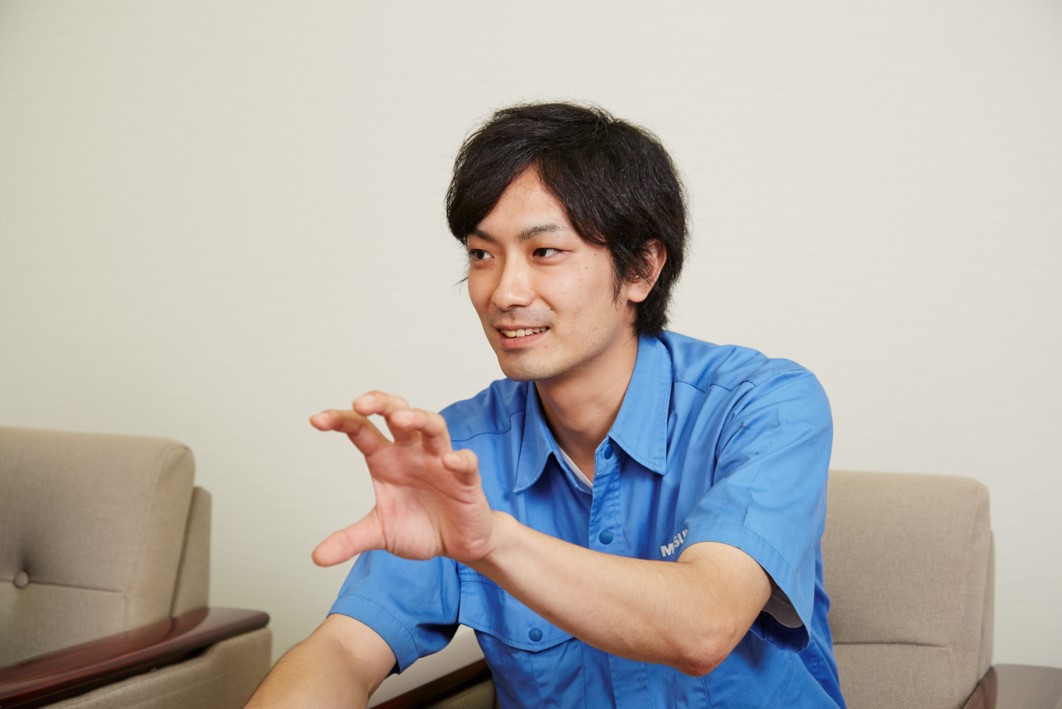
Hisato Ishiguro
Functional Development Team 2, Materials Technology Department,
Industrial Materials Technology Supervisory Department
I was told to move ahead on my own without regard to any preconceived notions, but when I started with the development I didn't have any preconceived notions to disregard. I was apprehensive at first, but recognized there would be more self-reproach in failing by not doing anything than in trying and failing, so went full steam ahead. The more I learned about rubber, the more I realized how little I know about the material. Coming up with theories without having any previous knowledge, I learned the importance of being able to develop theories on my own. By analyzing vast quantities of data, I learned about the correlations between rubber materials and belt properties, which was an important experience for me as an engineer. Going forward, I hope to go beyond rubber to learn more about all the materials used in belts so that I can take part in developing products that nobody else can emulate.
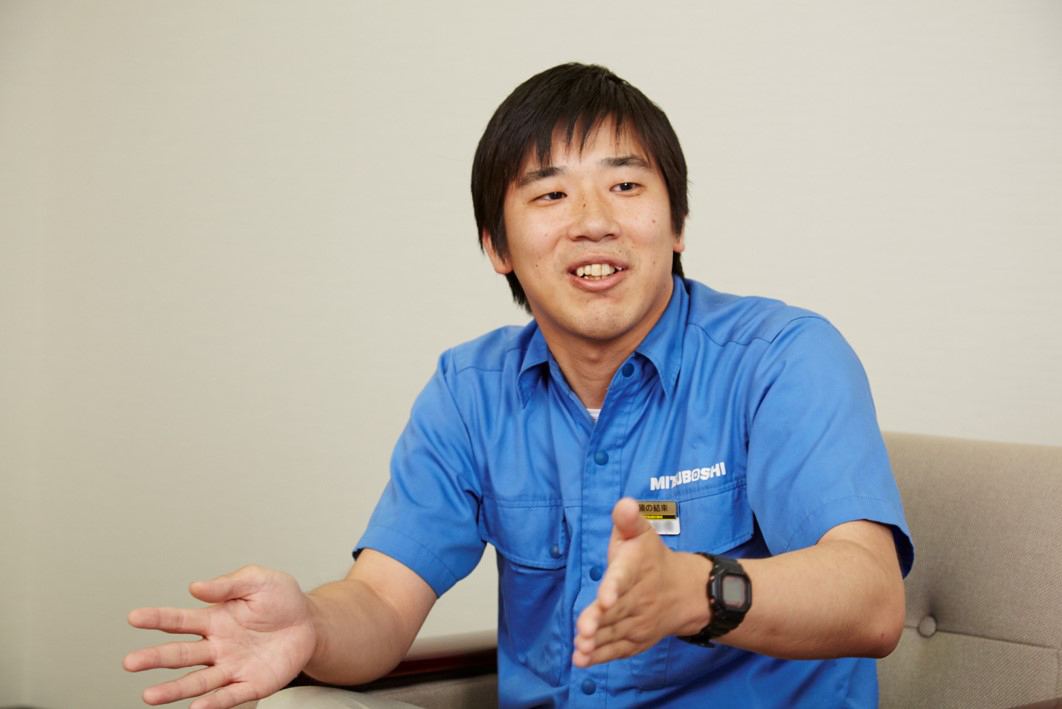
Hiroki Imai
Advanced Development Team, Product Technology Department 2,
Industrial Materials Technology Supervisory Department
I had little experience in product development, and sometimes I felt I couldn't tell left from right, but by working with highly experienced superiors I began to find my place on the team. Working every day on the factory production lines, it was my job to coordinate with the line and personnel to produce the belts for testing. I learned the importance of being able to communicate convincingly, not just within my team but also with production, sales and other departments. As a result, I think this project was a major boon to my growth as a person, as well as an engineer. Currently, I am working in product design with a new development department. I want to gain more knowledge about materials and learn about proposal-based manufacturing, the ability to create products having certain characteristics.
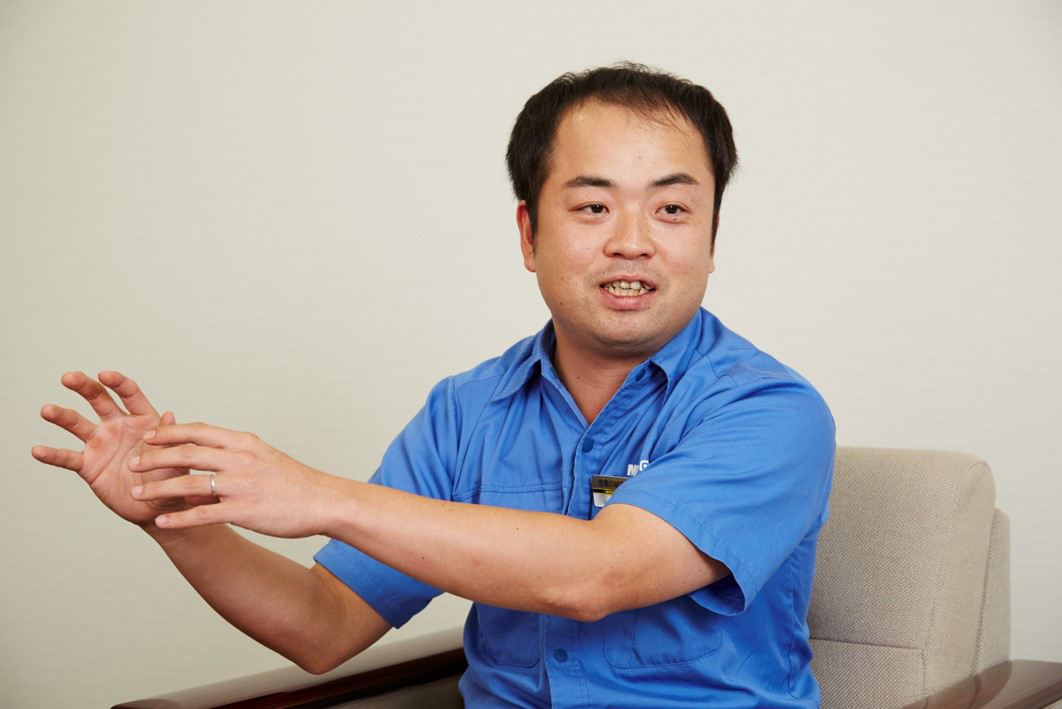
Takayuki Shige
Design Team 1, Product Technology Department 2,
Industrial Materials Technology Supervisory Department
When I was selected to join the development team, I had almost no experience in testing and assessment, but I felt a great sense of responsibility when I was told that testing for friction loss was being left up to me. I put my heart into coming up with accurate test results. At the point when we were getting close to meeting the customer's targets for standard losses, I realized anew that test results were not something to be taken lightly. I knew that if I was wrong, I would be seriously inconveniencing everybody. During our regular meetings, we determined the issues and considered specifically how each person would address the issues. Our roles were clear, and I went about my work with a heightened sense of awareness. I am currently working in product design, where I am in charge of responding to customer inquiries about Low Friction Loss Belts. I am pleased to be able to offer solutions with confidence.
Note: Departmental affiliates and histories with the Company are as of the time of development.